The Science Behind Homogeneous Mixture Creation for Consistent Results
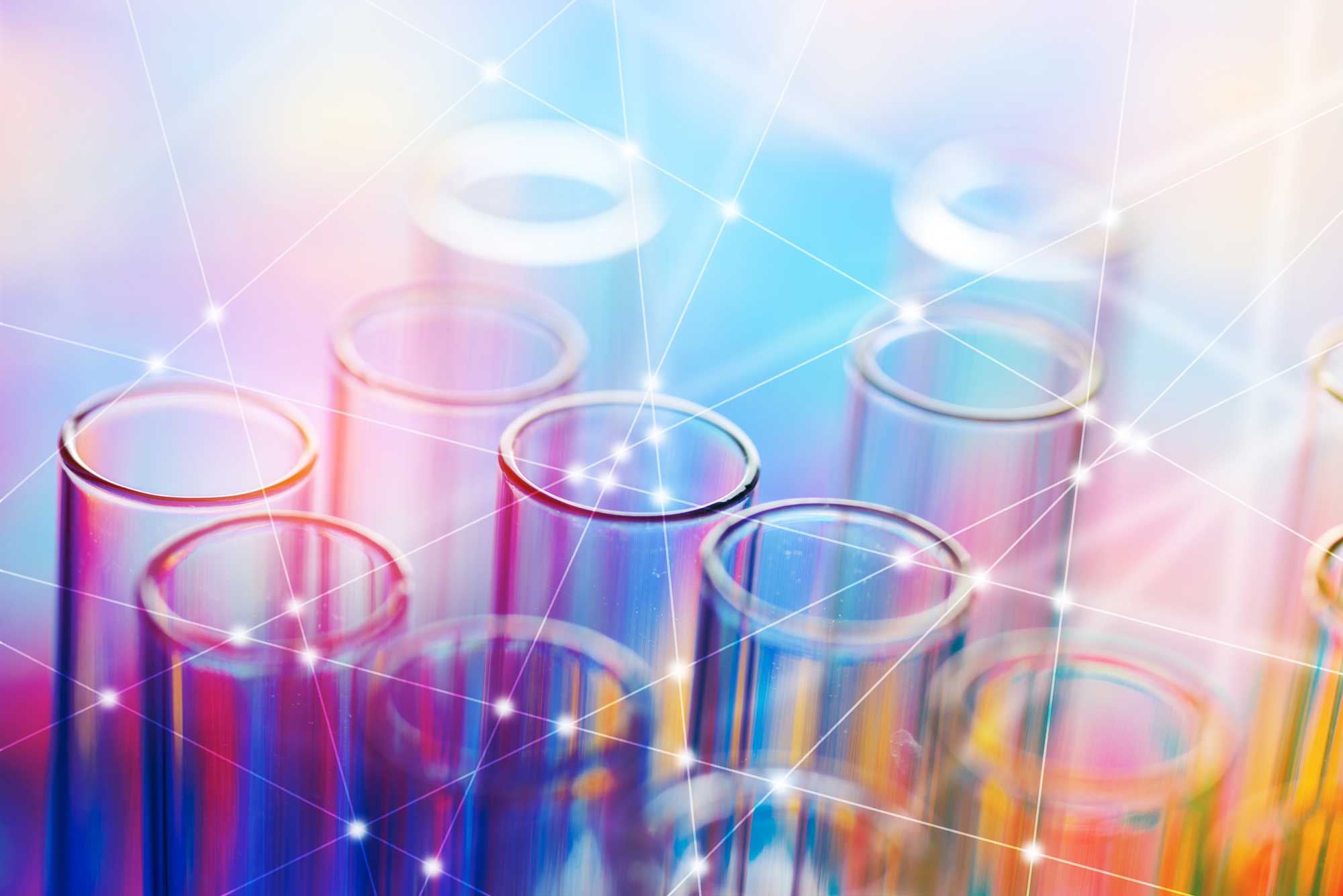
In the realm of industrial manufacturing and chemical formulation, consistency is not just a quality metric—it is the bedrock of customer satisfaction, regulatory compliance, and brand integrity. At the core of this consistency lies a deceptively complex scientific process: homogeneous mixture creation. While the term may appear straightforward, the science behind creating mixtures with uniform composition at the molecular or particulate level involves a precise balance of chemistry, process engineering, equipment selection, and quality assurance protocols.
Understanding What a Homogeneous Mixture Is
A homogeneous mixture is defined as a system in which the composition is uniform throughout. Whether in solid, liquid, or gas phases, each sample taken from a homogeneous mixture will contain the same ratio of components in the same state. Unlike heterogeneous mixtures, where distinct phases or layers can be observed, homogeneous mixtures appear as one continuous phase.
Some common examples include:
- Solutions such as saltwater or ethanol in water
- Alloys like brass (copper and zinc)
- Emulsions such as certain cosmetic formulations
- Gas blends like atmospheric air or industrial gas mixtures
Creating such uniformity at an industrial scale requires not just the right combination of materials but also precise control over environmental and mechanical variables during the blending process.
The Scientific Foundation: Key Variables in Mixture Homogeneity
To produce a consistently homogeneous mixture, several scientific principles must be meticulously managed:
1. Particle Size and Distribution
In solid-solid or solid-liquid systems, particle size significantly impacts blend uniformity. Smaller and more evenly sized particles are easier to mix thoroughly, reducing segregation potential. Milling or micronization may be necessary prior to blending.
2. Solubility and Intermolecular Forces
In liquid-liquid and solid-liquid mixtures, solubility governs the uniform dispersion of components. Understanding polar and non-polar interactions, hydrogen bonding, and Van der Waals forces helps in selecting compatible solvents and surfactants.
3. Viscosity and Flow Properties
High-viscosity materials can hinder diffusion and mass transfer, requiring elevated temperatures or high-shear mixing to ensure proper incorporation. Rheological properties must be understood and controlled.
4. Mixing Time and Energy Input
Insufficient mixing may result in localized concentration disparities. On the other hand, over-mixing can degrade sensitive ingredients or alter physical properties. Optimizing the duration and intensity of the mixing process is key.
5. Thermal Dynamics
Temperature influences solubility, reaction kinetics, and viscosity. Controlled heating and cooling cycles are often integral to maintaining blend consistency, especially in heat-sensitive formulations.
Mixing Technologies for Homogeneous Mixture Creation
Achieving homogeneous mixtures requires appropriate blending equipment that is tailored to the material state and process goals. At Industrial Technology Corporation, we utilize a range of technologies, each with its specific scientific advantages:
1. Ribbon Blenders
Ideal for dry powder mixing, ribbon blenders use helical ribbons rotating in opposite directions to achieve axial and radial mixing. These blenders offer high throughput with relatively gentle shear, suitable for free-flowing powders.
2. Paddle Blenders
More suitable for fragile or shear-sensitive materials, paddle blenders generate fluidized movement to ensure thorough but gentle mixing.
3. High-Shear Mixers
For emulsification and suspension of fine particulates, high-shear mixers introduce intense energy into the system. Rotor-stator systems are often employed to reduce particle sizes and promote dispersion in viscous media.
Each piece of equipment is selected based on the nature of the materials, batch size, sensitivity, and desired physical properties of the final product.
Quality Control: Testing for Mixture Uniformity
After blending, it is critical to verify that the mixture meets pre-defined homogeneity criteria. Industrial Technology Corporation follows rigorous quality control (QC) protocols to validate batch consistency:
1. Sampling Protocols
Randomized sampling from multiple points within the batch is performed to account for spatial variability. This is especially important for powders that may segregate due to gravity or electrostatic forces.
2. Analytical Testing
Techniques such as refractometry, fluid conductance, and cloud point. In some cases, titration or physical testing (e.g., density, viscosity) is also employed.
Challenges and Solutions in Homogeneous Mixture Creation
Even with sophisticated equipment and precise protocols, several challenges may arise in industrial blending operations:
Ingredient Incompatibility
Certain ingredients may react with each other or exhibit poor solubility, leading to phase separation or clumping. Industrial Technology Corporation tackles this through pre-formulation testing and the use of emulsifiers, dispersants, or pH modifiers.
Scaling from Lab to Production
Mixtures that perform well at the lab scale may behave differently in large production batches due to changes in flow dynamics or thermal gradients. Industrial Technology Corporation uses pilot-scale trials to bridge this gap and ensure scale-up success.
Batch-to-Batch Variation
Raw material inconsistencies or equipment wear can introduce variability. Our in-house QC and equipment maintenance schedules help eliminate such inconsistencies and ensure reliable performance.
Industrial Technology Corporation’s Approach to Precision Toll Blending
At Industrial Technology Corporation, homogeneous mixture creation is not a generic service—it’s a scientific discipline. Our custom toll blending services are rooted in:
- Scientific Expertise: Our chemists and process engineers collaborate on every formulation to optimize consistency, stability, and performance.
- Customized Formulations: Whether you need your proprietary blend scaled or a formulation developed from scratch, we tailor every solution to your needs.
- High-Capacity Equipment: With a versatile lineup of blenders, mixers, and reactors, we accommodate batch sizes from a few gallons to thousands of pounds.
Whether you’re operating in food, personal care, agriculture, or chemical manufacturing, Industrial Technology Corporation is your trusted partner for precision blending that delivers consistent, reproducible outcomes.
Why Consistency Is Non-Negotiable in Today’s Competitive Landscape
In today’s fast-paced industrial environment, customers and regulators alike demand repeatable performance. Any deviation in product composition can lead to customer dissatisfaction, product recalls, or costly compliance issues. That’s why homogeneous mixture creation is more than a technical goal—it’s a strategic imperative.
By partnering with Industrial Technology Corporation, you gain access to quality systems, and manufacturing capabilities that ensure your products are made right the first time—and every time.
Ready to Achieve Consistent, High-Quality Blends?
If your business depends on flawless mixture uniformity, precise formulations, and dependable production cycles, Industrial Technology Corporation is ready to help. Our custom toll blending services, private label manufacturing, and formulation expertise are designed to give your business a competitive edge.
Contact us today to request a quote, discuss your specifications, or explore new product possibilities. We look forward to working with you to develop innovative solutions that drive your business’s success.