In-Line Liquid Blending: Streamlining Efficiency in Continuous Processes
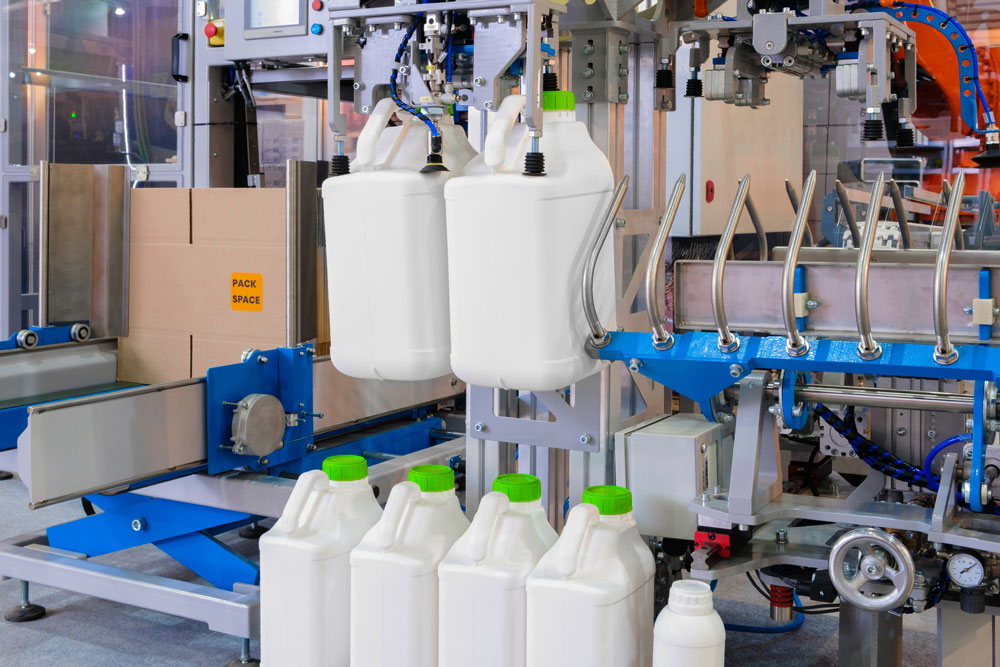
In today’s fast-paced industrial landscape, efficiency, precision, and scalability are key drivers of success. Manufacturers across multiple sectors are constantly seeking innovative solutions to improve production processes, reduce waste, and enhance product consistency. One such technology that has gained widespread adoption is in-line liquid blending—a method that offers significant advantages over traditional batch processing.
What Is In-Line Liquid Blending?
In-line liquid blending is a continuous process in which two or more liquid components are precisely mixed in a controlled environment as they flow through a system. Unlike batch processing, where ingredients are measured, mixed, and processed in fixed quantities, in-line blending provides a seamless, automated approach to fluid mixing, ensuring real-time control and adaptability.
How In-Line Liquid Blending Differs from Batch Processing
Batch processing has long been the conventional approach in manufacturing. It involves pre-measuring components, mixing them in a tank or vessel, and then processing the final mixture in stages. While effective, this method presents several challenges, including:
- Increased processing time due to the need for sequential operations.
- Higher material waste from residue left in mixing vessels.
- Limited scalability, as each batch size is predetermined.
- Inconsistent quality due to variations between batches.
In contrast, in-line liquid blending eliminates the need for holding tanks, allowing for on-the-fly adjustments, precise metering, and improved efficiency. It minimizes manual handling, reducing human error while ensuring consistency across production runs.
Core Principles of In-Line Blending Systems
An effective in-line liquid blending system relies on several key components:
- Flow Control and Measurement: Automated flow meters precisely regulate the input of each component.
- Mixing Modules: Static or dynamic mixers ensure uniform blending without the need for large mixing tanks.
- Automation and Control Systems: Advanced PLC (Programmable Logic Controller) systems monitor and adjust parameters such as flow rates, temperature, and viscosity.
- Quality Assurance Sensors: Real-time monitoring and feedback loops enable immediate corrections, ensuring adherence to formulation standards.
By leveraging these components, in-line blending systems provide manufacturers with a high level of control, efficiency, and repeatability in their blending operations.
Applications of In-Line Liquid Blending Across Industries
The versatility of in-line liquid blending makes it an indispensable technology across various industries. From food production to chemical and pharmaceutical manufacturing, the ability to streamline liquid mixing processes has transformed industrial operations.
Uses in Food and Beverage Production
In the food and beverage sector, maintaining flavor consistency, ingredient precision, and quality control is crucial. In-line blending is widely used in applications such as:
- Juice and Beverage Formulation: Precise blending of fruit concentrates, sweeteners, and preservatives ensures consistent taste profiles.
- Dairy Processing: Continuous mixing of milk, cream, and stabilizers optimizes product homogeneity.
- Flavor and Syrup Dispensing: Automated systems allow for rapid formulation changes, reducing downtime and production inefficiencies.
- Brewing and Fermentation: Consistent ingredient incorporation enhances product uniformity in beer and spirits production.
With in-line blending, food manufacturers can minimize waste, accelerate production cycles, and maintain strict compliance with industry regulations.
Role in Chemical and Pharmaceutical Manufacturing
For chemical and pharmaceutical industries, in-line liquid blending plays a critical role in ensuring precise chemical compositions, purity, and stability. Key applications include:
- Personal Care and Cosmetic Manufacturing: Consistent blending of oils, emulsifiers, and active ingredients enhances product performance.
- Industrial Chemicals and Coatings: In-line blending ensures accurate formulations of coatings, adhesives, and resins.
- Pharmaceutical API Blending: Active pharmaceutical ingredient (API) solutions require precise dosage control, which in-line blending facilitates.
- Sanitizers and Disinfectants: The COVID-19 pandemic underscored the importance of rapid and scalable sanitizer production, an area where in-line blending excels.
With automated process control and real-time monitoring, manufacturers in these industries can achieve greater regulatory compliance while maintaining cost-effective production.
Advantages of In-Line Blending for Continuous Processes
The transition from batch processing to in-line blending offers several significant advantages. By eliminating the inefficiencies of traditional methods, companies can experience greater productivity, cost savings, and sustainability improvements.
Reducing Waste and Enhancing Consistency
One of the primary benefits of in-line liquid blending is its ability to minimize material waste. Unlike batch processing, which often results in excess product and unused raw materials, in-line blending precisely meters the exact amount needed, reducing overproduction.
Additionally, real-time monitoring ensures:
- Uniform product quality across production runs.
- Lower risk of contamination, as materials are mixed in a closed system.
- Enhanced shelf stability, due to improved homogeneity of blended liquids.
By eliminating batch-to-batch variability, manufacturers can ensure higher quality control standards and increased customer satisfaction.
Scalability and Cost Savings for Modern Operations
Scalability is a crucial factor in today’s competitive market, and in-line blending offers unmatched flexibility for companies looking to expand production.
Key Cost-Saving Benefits:
- Lower energy consumption: Continuous processing reduces heating and cooling cycles, saving energy costs.
- Reduced labor costs: Automated control systems require fewer manual interventions.
- Faster production rates: On-demand blending eliminates bottlenecks in production lines.
- Lower equipment footprint: Without the need for large batch tanks, facility space can be optimized for efficiency.
By integrating in-line liquid blending into continuous process workflows, businesses can scale efficiently without sacrificing quality.
Optimize Your Operations with Industrial Technology Corporation
As industries continue to push for higher efficiency, in-line liquid blending stands out as a game-changing solution for streamlining continuous processing. Whether in food production, chemical formulation, or pharmaceutical manufacturing, this technology enables precise blending, waste reduction, and cost-effective scalability.
If your business is seeking custom toll blending services, private label opportunities, or top-tier chemical formulations, Industrial Technology Corporation is ready to meet your needs. With industry expertise and cutting-edge solutions, we provide tailored blending services that optimize production while ensuring quality and consistency.
Contact us today to inquire about our services, request a quote, or discuss your specific requirements. Let us help you develop innovative solutions that drive your business’s success.