Navigating Supply Chain Challenges in Custom Chemical Formulation
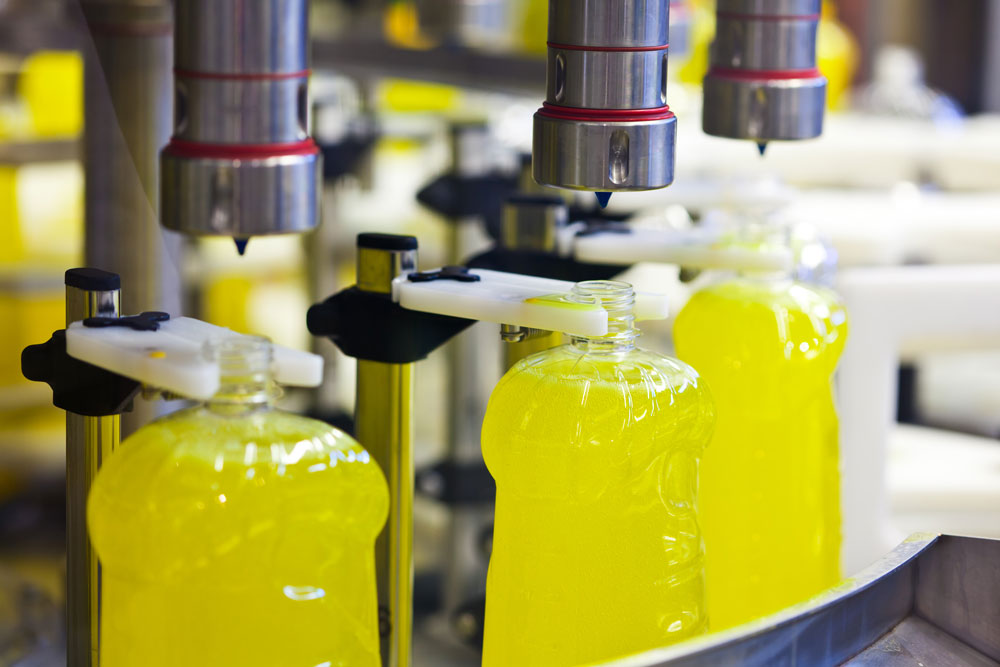
In the realm of specialty chemicals, custom chemical formulation is a precision-driven process that demands stringent quality control, regulatory compliance, and timely execution. Underpinning all these elements is a robust system of supply chain management — the backbone that ensures raw materials, production schedules, and customer deliveries are harmoniously aligned. As industries become more global and complex, managing the supply chain in custom chemical formulation is increasingly fraught with challenges.
Understanding Supply Chain Dynamics in Chemical Formulation
Custom chemical formulation involves tailoring chemical blends to meet specific client needs, often in highly regulated industries such as pharmaceuticals, agriculture, food processing, and industrial manufacturing. The formulation process itself is complex and requires the integration of diverse components, including raw material sourcing, batch testing, regulatory documentation, quality assurance, and distribution logistics.
Supply chain dynamics in this context differ markedly from traditional manufacturing:
- Diversity of Materials: Custom formulations typically require a wide range of raw materials, many of which may be rare, volatile, or subject to regulatory restrictions.
- Variable Demand: Unlike mass production, customer-specific formulations may be ordered in small batches, leading to unpredictable demand patterns.
- Compliance Requirements: Regulatory compliance adds another layer of complexity, requiring transparent documentation and secure handling practices throughout the supply chain.
- Time Sensitivity: Delays in any stage — from procurement to transportation — can cascade into significant production lags and customer dissatisfaction.
In essence, the chemical formulation supply chain is a delicate balance of science, logistics, and risk management.
Common Challenges and Mitigation Strategies
The nature of the chemical industry makes its supply chain uniquely susceptible to disruptions. Here are some of the most prevalent challenges and recommended strategies to address them:
1. Raw Material Volatility
Many chemical inputs are derived from petrochemicals or agricultural feedstocks, both of which are vulnerable to price and supply fluctuations due to geopolitical tensions, natural disasters, or market dynamics.
Mitigation Strategies:
- Diversify the supplier base to avoid over-reliance on a single source.
- Establish long-term contracts with key suppliers to lock in pricing and availability.
- Implement hedging strategies for critical raw materials to manage cost risks.
2. Regulatory Hurdles
Stringent regulations govern the handling, storage, and transportation of chemical substances, such as OSHA, REACH, TSCA, and others. Non-compliance can result in shipment delays or legal penalties.
Mitigation Strategies:
- Maintain a centralized compliance management system that tracks evolving regulatory requirements.
- Invest in training for logistics and procurement teams on chemical safety and legal obligations.
- Work with regulatory experts or consultants who can offer proactive guidance.
3. Logistics Disruptions
Global transportation networks are frequently disrupted by port congestion, political unrest, or pandemics. These disruptions can stall the timely delivery of raw materials or finished products.
Mitigation Strategies:
- Maintain a buffer stock of essential inputs based on risk assessments.
- Leverage multi-modal transportation options to reduce dependence on a single shipping route.
- Employ supply chain visibility tools to track shipments in real-time and adjust plans as needed.
4. Quality Control
The inconsistency in raw material quality can have a cascading effect on the final product’s performance, leading to rejected batches and costly recalls.
Mitigation Strategies:
- Implement robust incoming inspection protocols for all raw materials.
- Establish supplier audits and performance scorecards.
- Use statistical process control (SPC) methods to monitor production consistency.
5. Demand Variability
Uncertain demand patterns for custom formulations can result in either overstocking or stockouts, each carrying its own financial risks.
Mitigation Strategies:
- Collaborate closely with clients to forecast demand more accurately.
- Use flexible manufacturing setups that can scale up or down based on order volume.
- Implement just-in-time (JIT) inventory systems to minimize waste while ensuring availability.
Tools and Technologies for Efficient Supply Chain Management
To overcome the above challenges, chemical formulators must leverage modern tools and technologies that provide visibility, control, and predictive power.
Enterprise Resource Planning (ERP) Systems
ERP systems integrate procurement, inventory, production, and distribution data in a centralized platform. For chemical manufacturers, an ERP tailored to process industries can effectively manage batch tracking, regulatory documentation, and formula version control.
Advanced Planning and Scheduling (APS)
APS software allows for real-time scheduling and resource allocation based on demand and capacity constraints. This is particularly important for facilities handling multiple custom blends with varying priorities.
Internet of Things (IoT) and Sensors
IoT-enabled equipment can track parameters such as temperature, pressure, and humidity in real-time during chemical processing and storage. This ensures compliance and enhances quality assurance.
Blockchain for Supply Chain Transparency
Blockchain technology offers a tamper-proof way to log transactions, certifications, and chain-of-custody records. This is vital for chemicals that require traceability across global networks.
Artificial Intelligence (AI) and Predictive Analytics
AI-powered platforms can predict demand, flag potential disruptions, and optimize procurement schedules using historical and real-time data. This enhances agility and responsiveness in supply chain decision-making.
Supplier Relationship Management
Strong relationships with suppliers are foundational to a resilient chemical supply chain. These relationships go beyond price negotiations — they encompass collaboration, transparency, and mutual growth.
Best Practices:
- Conduct joint planning sessions with suppliers to anticipate material needs and mitigate shortages.
- Share performance metrics and improvement goals regularly.
- Develop contingency contracts that ensure priority allocation in times of scarcity.
Chemical formulators should view their suppliers as strategic partners, not just transactional vendors.
Inventory and Demand Forecasting
Accurate forecasting is critical to maintaining the delicate balance between availability and cost efficiency. Traditional forecasting models often fall short in the face of customization and demand variability.
Approaches to Improve Forecasting:
- Integrate client order histories and industry trends into forecasting algorithms.
- Use machine learning models to identify patterns in customer behavior.
- Monitor macroeconomic and geopolitical indicators that may affect supply and demand.
Additionally, scenario planning — where multiple demand and supply situations are modeled — can help decision-makers prepare for uncertainties.
Case Studies of Supply Chain Optimization
Case Study 1: Dual-Sourcing Strategy Saves the Day
A mid-sized toll blender faced raw material shortages when its primary supplier in East Asia experienced shutdowns due to geopolitical tensions. By proactively developing a dual-sourcing strategy, the company was able to shift procurement to a secondary supplier in North America without affecting production schedules.
Results:
- Maintained uninterrupted production.
- Strengthened supplier diversification.
- Enhanced reputation with clients for reliability.
Case Study 2: IoT Integration Enhances Storage Safety
An industrial chemical formulation facility integrated IoT sensors across its bulk storage tanks to monitor critical parameters in real-time. Alerts were set up for temperature thresholds and chemical compatibility risks.
Results:
- Zero incidents reported in 18 months.
- Reduced insurance premiums due to improved risk management.
- Streamlined compliance reporting with automated logs.
Case Study 3: AI-Driven Forecasting Boosts Efficiency
A custom blend manufacturer adopted AI-powered demand forecasting tools to replace its manual Excel-based approach. By integrating client sales data and external market indicators, it could predict seasonal spikes with 85% accuracy.
Results:
- Reduced inventory holding costs by 22%.
- Improved customer service levels.
- Cut backorder occurrences by 40%.
Ensuring a Resilient Future for Chemical Formulators
Navigating the complexities of supply chain management in custom chemical formulation demands a multi-faceted approach. It requires foresight, technology integration, regulatory awareness, and strong partnerships across the value chain. As the industry becomes more global and customer expectations rise, supply chain resilience will define competitive advantage.
Industrial Technology Corporation understands the stakes. Whether you’re in need of custom toll blending services, private label opportunities, or quality chemical formulations for your business, we are here to meet your needs. Simply contact us today to inquire about our services, request a quote, or discuss your specific requirements. We look forward to working with you to develop innovative solutions that drive success for your business.