What Is Industrial Ribbon Blender Technology & Its’ Key Benefits?
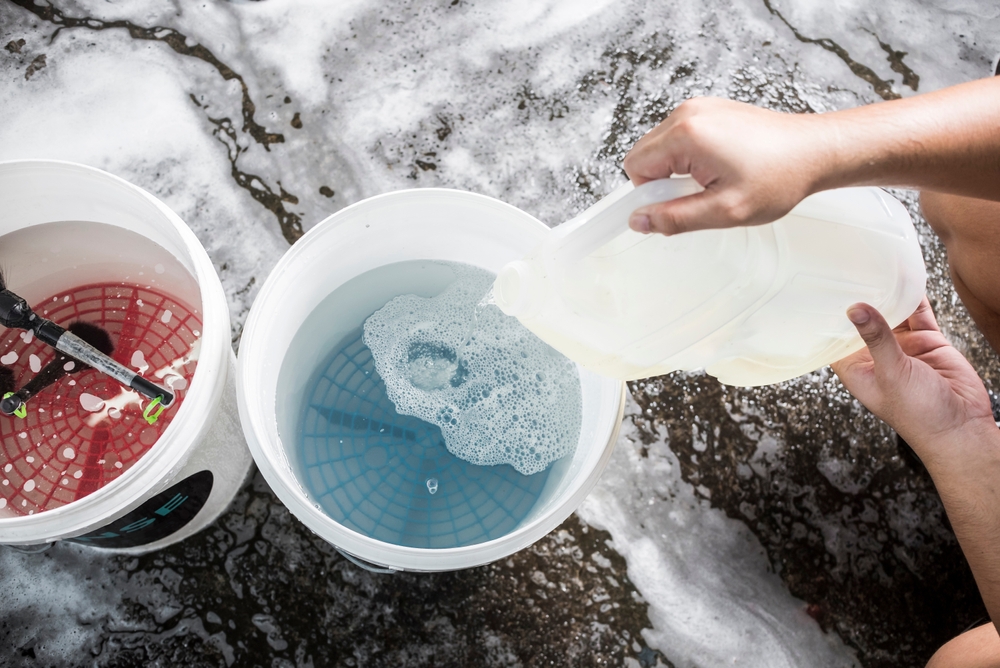
In the world of industrial mixing and blending, industrial ribbon blender technology stands as a cornerstone for producing uniform, homogenous mixtures at scale. Whether it’s for pharmaceuticals, food ingredients, chemicals, plastics, or cosmetics, ribbon blenders offer an efficient, versatile solution for powder and bulk solid mixing. Their simplicity of design, reliable performance, and scalability have made them a standard in manufacturing facilities around the globe.
Understanding Industrial Ribbon Blender Technology
What Is an Industrial Ribbon Blender?
An industrial ribbon blender is a type of industrial mixer consisting of a horizontal U-shaped trough and a set of inner and outer helical ribbons mounted on a horizontal shaft. These ribbons rotate to create a convective mixing action that combines materials in a consistent and efficient manner. The design ensures thorough blending by moving materials both radially and laterally within the trough.
The inner ribbon moves material in one direction, while the outer ribbon moves it in the opposite direction. This counter-current movement enhances blending uniformity, making ribbon blender technology ideal for mixing solid-solid, solid-liquid, and even viscous materials under certain configurations.
Core Components of an Industrial Ribbon Blender
A standard industrial ribbon blender is composed of several key parts:
- Trough (Mixing Chamber): The vessel where materials are placed. Typically fabricated from stainless steel for easy cleaning and corrosion resistance.
- Shaft with Ribbon Agitators: A centrally mounted shaft supports the inner and outer helical ribbons. These are precision-engineered for optimal mixing efficiency.
- Drive System: Usually a motor and gearbox that control the rotation speed of the shaft and ribbons.
- Discharge Valve: Located at the bottom of the trough, this allows for fast and complete discharge of blended material.
- End Seals and Bearings: Designed to prevent product leakage and ensure smooth operation over extended periods.
Advanced systems may also include additional features like spray bars for liquid addition, high-speed choppers to break down agglomerates, and jacketed troughs for heating or cooling.
How Industrial Ribbon Blender Technology Works
Ribbon blender technology relies on a combination of axial and radial movements. When the ribbons rotate:
- Radial Mixing: Material near the shaft is moved outward, while material near the wall is pulled inward.
- Axial Mixing: The outer ribbon moves material from the ends of the blender toward the center, while the inner ribbon moves material from the center toward the ends.
This dual-flow mechanism results in a turbulent zone where materials are repeatedly split, moved, and recombined, thus achieving a homogeneous blend in a relatively short time. Mixing cycles vary depending on the product’s characteristics but typically range from 10 to 15 minutes.
Key Benefits of Ribbon Blender Technology
1. Uniform Mixing Quality
The primary advantage of ribbon blender technology is its ability to achieve a high degree of homogeneity—often within 90–95% uniformity—in a short period. This consistency is vital in industries like pharmaceuticals and food processing, where product quality and regulatory compliance are critical.
2. High Efficiency and Throughput
Ribbon blenders can handle large batch sizes, ranging from a few liters to several thousand liters, making them suitable for both small-batch and full-scale production. The relatively fast mixing time also translates to higher throughput, supporting tight production schedules.
3. Versatility
These blenders can process a wide range of materials—powders, granules, pellets, pastes, and even low-viscosity liquids. This versatility makes them a preferred choice for multiproduct facilities that require frequent changeovers.
4. Gentle Blending Action
Despite their efficiency, ribbon blenders offer a gentle mixing mechanism, which is crucial for blending fragile or shear-sensitive ingredients without breaking down particle structure.
5. Ease of Cleaning and Maintenance
The straightforward design of ribbon blenders facilitates easy cleaning, which is essential for minimizing cross-contamination and maintaining batch integrity. Many systems also feature quick-release end plates and easily accessible internal components.
6. Cost-Effective Operation
Compared to other high-shear or high-energy mixers, ribbon blenders consume relatively less power and require minimal operator supervision, reducing operational costs over time.
Common Applications of Ribbon Blender Technology
1. Pharmaceuticals
Ribbon blenders mix active pharmaceutical ingredients (APIs) with excipients, powders for capsules, granules for tablets, and other dry formulations. Their ability to achieve consistent blending ensures dosage uniformity, which is vital for drug efficacy and patient safety.
2. Food and Beverage
From spice mixes and flavorings to baking powders and instant drink formulations, ribbon blenders provide a hygienic and efficient method for producing food-grade blends. Their stainless-steel construction meets stringent food safety standards, and optional liquid spray systems can be used for flavor or color infusion.
3. Chemical Manufacturing
In the chemical industry, ribbon blenders are employed to mix dry chemicals, resins, polymers, and catalysts. Their rugged design allows for the safe handling of abrasive or reactive materials.
4. Cosmetics and Personal Care
Products such as facial powders, bath salts, and powdered cleansers benefit from the uniform distribution of active ingredients enabled by ribbon blender technology. These mixers can also accommodate light moistures, fragrances, and oils when paired with appropriate liquid addition systems.
5. Plastics and Rubber
Ribbon blenders are used to combine fillers, colorants, and plasticizers with polymer bases. Their consistent mixing action helps ensure product uniformity and facilitates downstream processing.
6. Agricultural Products
Animal feeds, pesticides, herbicides, and seed treatments often require precise mixing of multiple ingredients. Ribbon blenders provide the consistency needed for safe and effective application in the agricultural sector.
Ribbon Blender Configurations and Customizations
To accommodate diverse product requirements, ribbon blenders can be custom-designed with a variety of features, including:
- Variable Speed Drives: Allow fine-tuning of the mixing process for different materials.
- Vacuum Systems: Enable deaeration or solvent removal during blending.
- Jacketed Troughs: Permit thermal regulation through heating or cooling media.
- Sanitary Designs: Include polished surfaces, FDA-compliant seals, and easy-clean configurations for hygiene-critical industries.
- Explosion-Proof Designs: Essential for handling flammable or combustible materials.
Working with a manufacturer or toll blending provider that understands your process needs can help you select and optimize the right configuration.
Choosing the Right Ribbon Blender Provider
When investing in ribbon blender technology—whether through equipment purchase or outsourcing via toll blending services—it’s essential to partner with an experienced, knowledgeable provider. Key factors to evaluate include:
- Experience and Industry Knowledge: Providers with deep experience across multiple industries can better understand and meet your specific formulation requirements.
- Customization Capabilities: The ability to adapt equipment for your material characteristics is vital to achieving optimal results.
- Scalability: Providers should offer flexible batch sizes to support both development-scale and commercial-scale production.
- Technical Support: Ongoing assistance for troubleshooting, process optimization, and equipment maintenance adds long-term value.
The Role of Ribbon Blenders in Toll Blending
Toll blending services utilize ribbon blender technology to offer businesses a cost-effective alternative to in-house manufacturing. By outsourcing blending and packaging needs, companies can:
- Focus on core competencies like R&D and marketing
- Eliminate capital investments in expensive mixing equipment
- Maintain production flexibility without facility constraints
- Reduce overhead associated with regulatory compliance and staffing
At Industrial Technology Corporation, we specialize in delivering advanced toll blending solutions using ribbon blenders tailored to various industries and product types.
Why Choose Industrial Technology Corporation?
Industrial Technology Corporation has earned a reputation for excellence in custom chemical blending and formulation. Our use of ribbon blender technology allows us to serve clients across a wide spectrum of industries with unmatched precision and reliability.
Our services include:
- Custom Toll Blending: Scalable and cost-effective, whether you need small batches or full-scale production.
- Private Label Manufacturing: Let us produce and package your branded products with confidentiality and consistency.
- Advanced Chemical Formulations: Our experienced team works closely with you to develop blends that meet exact specifications.
Contact Us Today
Whether you need custom toll blending services, private label opportunities, or quality chemical formulations for your business, Industrial Technology Corporation is here to meet your needs. We combine years of industry experience with ribbon blender technology to ensure every batch meets your performance and quality expectations.
Contact us today to inquire about our services, request a quote, or discuss your specific requirements. We look forward to working with you to develop innovative solutions that drive your business’s success.