Precision Chemical Formulation: The Science Behind Multi-Component Blending
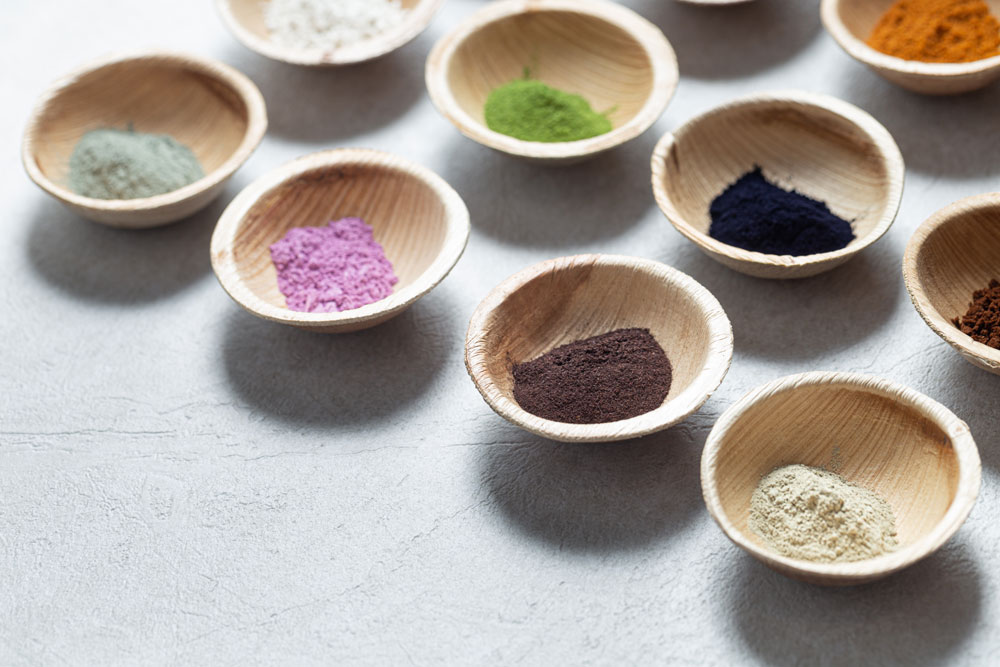
In the world of chemical manufacturing, precision is not just a requirement—it’s the cornerstone of successful production. Multi-component blending, the intricate process of combining multiple chemical substances into a homogeneous mixture, is an essential technique in industries ranging from pharmaceuticals to agriculture.
What Is Multi-Component Blending?
Multi-component blending refers to the process of combining two or more chemical components to produce a finished product or intermediate material with specific properties. Depending on the formulation, the components may include liquids, solids, or gases. The goal is to achieve uniformity and maintain the desired chemical and physical characteristics, ensuring the end product meets quality standards and functional requirements.
Industries utilizing multi-component blending span diverse sectors, such as:
- Pharmaceuticals for drug formulations
- Agriculture for fertilizers and pesticides
- Automotive for lubricants and fuels
- Food and Beverage for flavorings and additives
- Industrial Chemicals for coatings, adhesives, and sealants
The Core Principles of Multi-Component Blending
Achieving precision in multi-component blending involves adhering to several scientific and engineering principles:
Proportional Accuracy
To maintain the integrity of the final formulation, each component must be measured with exacting precision, often to milligram or microliter levels. Small deviations can result in defective products or unintended reactions.
Homogeneity
Homogeneity ensures that every portion of the mixture contains the same ratio of components. Achieving this requires advanced mixing technologies and expertise in material properties.
Stability
Stability ensures the blended components do not separate or degrade over time. Stabilizing agents, temperature control, and careful handling are often necessary to maintain product consistency.
Reactivity
Some chemical components interact during blending, requiring precise control over reaction conditions such as temperature, pressure, and mixing speed to avoid undesired outcomes.
Technologies Used in Multi-Component Blending
Advances in technology have significantly enhanced the efficiency and precision of multi-component blending. Here are some of the key tools and methodologies employed:
Mixing Equipment
From high-shear mixers to ribbon blenders, the choice of equipment depends on the nature of the materials and the desired product characteristics. For example:
- Ribbon Blenders are ideal for dry powders.
- High-Shear Mixers handle viscous liquids and emulsions.
- Static Mixers are used for continuous blending of fluids.
Automation and Control Systems
Modern blending facilities often incorporate automated systems equipped with sensors and software for real-time monitoring. Automation ensures consistent proportions, reduces human error, and provides traceable records for quality assurance.
Analytical Testing
Technologies such as spectroscopy, chromatography, and particle size analysis verify the blend’s composition and homogeneity. These tests ensure compliance with regulatory and industry standards.
Challenges in Multi-Component Blending
Despite technological advancements, multi-component blending presents several challenges that demand technical expertise and innovative solutions:
Complex Formulations
Some formulations involve dozens of components with varying physical and chemical properties. Managing these complexities requires in-depth knowledge of material science and chemical interactions.
Contamination Control
Cross-contamination can compromise the integrity of a blend, particularly in sensitive industries such as pharmaceuticals and food production. Strict cleaning protocols and specialized equipment designs mitigate this risk.
Environmental Factors
Temperature, humidity, and air quality can affect blending processes. For instance, hygroscopic materials may absorb moisture from the air, altering the final product.
Regulatory Compliance
Blended products must meet stringent industry and governmental regulations, which vary depending on the application. Compliance often involves detailed documentation and validation processes.
Case Studies: Applications of Multi-Component Blending
Pharmaceutical Formulations
In pharmaceutical manufacturing, multi-component blending is critical for producing drugs with precise dosages. Blends must achieve exact particle size distributions and maintain chemical stability, especially for controlled-release medications.
Agricultural Products
Fertilizers and pesticides rely on multi-component blending to combine active ingredients with carriers or stabilizers. Uniform distribution of active compounds ensures effectiveness and minimizes waste.
Coatings and Adhesives
Paints, coatings, and adhesives require multi-component blending to create formulations with specific viscosity, drying times, and durability. The inclusion of stabilizers and dispersants is essential for long-term performance.
Best Practices for Multi-Component Blending
Pre-Formulation Studies
Conducting pre-formulation studies helps identify potential issues, such as incompatibilities between components or the need for specific stabilizers.
Pilot Batches
Producing small pilot batches allows manufacturers to test and refine the blending process before scaling up to full production.
Quality Control
Regular testing during and after blending ensures the product meets specifications. Inline monitoring systems can provide real-time data, enabling immediate adjustments.
Custom Solutions
Partnering with a toll blending provider like Industrial Technology Corporation enables businesses to access custom solutions tailored to their unique needs.
Environmental and Economic Considerations
Sustainability and cost-effectiveness are increasingly important in multi-component blending. Strategies to address these considerations include:
- Optimizing Processes to reduce energy and material waste.
- Recycling Solvents and By-Products to minimize environmental impact.
- Sourcing Sustainable Materials for greener formulations.
Why Partner with a Toll Blending Expert?
Outsourcing multi-component blending to a toll blending expert provides numerous advantages, including access to specialized equipment, technical expertise, and scalable production capabilities. Toll blending partners also handle regulatory compliance, freeing businesses to focus on innovation and market expansion.
Contact Us Today
Whether you’re developing a new product or optimizing an existing formulation, multi-component blending requires precision, expertise, and advanced technology. At Industrial Technology Corporation, we specialize in custom toll blending services, private label opportunities, and high-quality chemical formulations tailored to meet your needs.
Contact us today to request a quote, discuss your specific requirements, or explore how our innovative solutions can drive success for your business. Let us be your partner in precision blending!