Powder Blending Mastery: Achieving Homogeneity in Industrial Mixtures
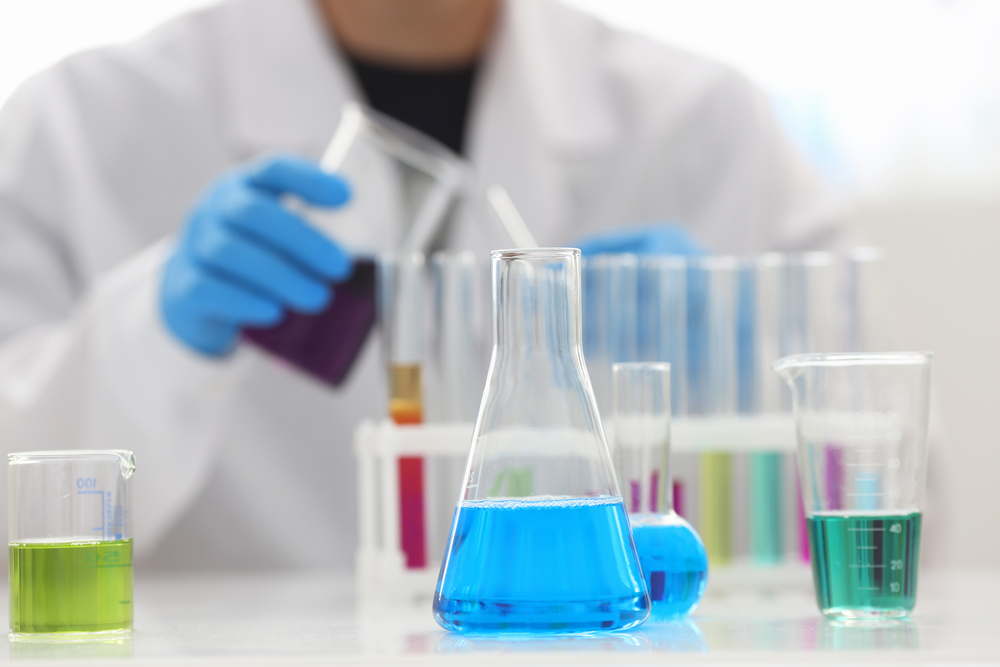
Powder blending plays a critical role in industries ranging from food production to chemical manufacturing and metallurgy. Achieving homogeneity in powder mixtures is essential for product consistency, performance, and safety, making powder blending a precise science that demands the right equipment, techniques, and understanding of material properties.
The Importance of Homogeneity in Powder Blending
Homogeneity, or uniform distribution of components within a mixture, is vital in industrial powder blending for a variety of reasons. Unevenly blended powders can lead to inconsistencies in product performance, which can impact safety, effectiveness, and customer satisfaction. For example, in industries such as chemicals and metallurgy, homogeneity is essential for predictable and reliable product properties.
The process of powder blending, however, is far from simple. Each powder blend requires unique handling based on the physical and chemical characteristics of its components, along with the specific demands of the application. Achieving true homogeneity depends on a combination of advanced equipment, an understanding of material science, and meticulous blending techniques.
Understanding the Fundamentals of Powder Blending
To master powder blending, it’s essential to understand the different mechanisms of mixing and how they interact with powder characteristics. Powder blending occurs through three primary mechanisms:
- Diffusion – The movement of particles to fill gaps between other particles, resulting in a gradual mixing effect.
- Shear – The sliding motion of particles over each other, which promotes dispersion and is especially effective for reducing agglomerates.
- Convective Mixing – The macroscopic movement of particles within the mixer, such as tumbling or rotating, that enables large-scale blending.
Each mixing mechanism contributes differently to homogeneity, depending on the physical properties of the powder materials, including particle size, density, shape, and flowability. Selecting the correct blending mechanism, or a combination of them, is key to producing a homogeneous mix.
Key Factors Influencing Homogeneity in Powder Blending
Achieving optimal powder blending requires careful consideration of several critical factors that can impact homogeneity:
Particle Size and Distribution
The size and distribution of particles within a powder mixture can significantly influence how well the blend will homogenize. Powders with a wide particle size distribution are more challenging to blend uniformly, as smaller particles may segregate or settle at the bottom of the mixture. In contrast, powders with similar-sized particles blend more uniformly and require less processing time to achieve homogeneity. Choosing the right particle size and ensuring a narrow size distribution can simplify blending and improve uniformity.
Bulk Density and Cohesiveness
Powder bulk density impacts how particles behave during blending. Dense powders with high cohesiveness are prone to clumping, leading to uneven distribution. In contrast, low-density, free-flowing powders are more manageable and tend to blend evenly. Controlling bulk density through pre-processing techniques, such as granulation, can make blending easier and more effective for cohesive powders.
Flow Properties
The flowability of powders is critical for efficient blending. Powders with poor flow characteristics, often caused by high cohesion or electrostatic charges, can form clumps and resist uniform mixing. Improving flow properties through the addition of flow aids, drying, or surface treatments can enhance the blend’s homogeneity.
Environmental Conditions
Humidity, temperature, and even air pressure can influence powder properties during blending. Humidity, for instance, can cause powders to clump or become sticky, complicating the blending process. Implementing controlled environmental conditions and using specialized equipment can help mitigate these effects, ensuring that the blending process remains consistent.
Choosing the Right Blending Equipment
Selecting the appropriate blending equipment is fundamental to achieving homogeneity. Equipment should be matched not only to the materials but also to the scale and precision required for the application. The primary types of blenders used in powder blending include:
V-Blenders
V-blenders are common in industries requiring high-quality mixing with minimal material degradation. The V-shaped design allows powders to tumble freely, making it particularly suitable for delicate powders and applications requiring gentle mixing. However, V-blenders may not be suitable for highly cohesive powders, as they lack the shear force needed to break up clumps.
Ribbon Blenders
Ribbon blenders are versatile and commonly used in industries requiring rapid, large-batch blending. The helical ribbons within the blender provide both convective and shear mixing, making them effective for blending powders of varying properties. Ribbon blenders are also adept at handling dense and cohesive powders, making them suitable for various industrial applications.
Turbula Mixers
Turbula mixers are used when a high degree of precision is required. These mixers provide three-dimensional movement, which ensures thorough blending, especially for powders with challenging properties. Turbula mixers are popular due to their high precision, but they are also used in other applications requiring exact homogeneity.
Fluidized Bed Blenders
In fluidized bed blending, air is forced through the powder bed, creating a “fluidized” state that allows particles to move freely. This method is suitable for very fine, free-flowing powders and provides uniform mixing with minimal energy. However, fluidized bed blenders are not suitable for cohesive powders or blends requiring intensive shear.
Optimizing Blending Parameters for Maximum Homogeneity
Achieving the ideal blend depends not only on choosing the right equipment but also on optimizing operational parameters. These parameters include:
Blending Time
The duration of blending is a critical parameter for achieving homogeneity. Too little blending time may result in incomplete mixing, while excessive blending can lead to particle breakage, segregation, or even degradation of sensitive powders. Determining the optimal blending time requires balancing particle properties, blender type, and desired outcome, often achieved through empirical testing.
Blender Speed and RPM
The rotation speed or RPM of a blender affects how particles move within the equipment. For example, higher RPMs increase shear and impact forces, which can help reduce clumping in cohesive powders. However, excessive RPMs can generate excessive heat and static electricity, potentially leading to segregation or material degradation. Adjusting blender speed based on powder characteristics can prevent these issues and improve homogeneity.
Filling Ratio
The fill level of a blender impacts how particles interact and move within the equipment. Under-filled blenders may not achieve sufficient mixing, while over-filled blenders can reduce blending efficiency. Optimal filling ratios vary by blender type but generally fall within 50-70% of the blender’s capacity to allow adequate particle movement and mixing.
Addition Sequence of Ingredients
The order in which powders are added can also impact blending success. Adding fine powders to a bed of coarse powders or introducing flow aids at specific intervals during blending can improve homogeneity. Developing an appropriate ingredient addition sequence can minimize agglomeration and maximize dispersion within the blend.
Advanced Powder Blending Techniques and Innovations
The demand for precise and efficient blending has led to the development of advanced techniques and technologies that enhance powder blending capabilities:
Continuous Blending
Continuous blending is an emerging technology that allows powders to be mixed in a continuous stream rather than batch-by-batch. This approach is advantageous for large-scale industrial processes that require high throughput and consistent product quality. Continuous blending systems are designed with feedback loops and sensors that monitor blend homogeneity in real-time, adjusting parameters as needed to maintain uniformity.
High-Shear Blending
High shear blending incorporates a mixing blade that operates at high speeds to break down clumps and achieve fine particle dispersion. This method is particularly useful for cohesive powders that resist traditional blending techniques. High-shear blenders can achieve homogeneity in less time than conventional blenders, making them a valuable option for industries requiring fast production cycles.
Precision Dosing and Dispersion Technology
Advancements in precision dosing technology enable powders to be added to blends in exact proportions, enhancing consistency and reducing waste. Combined with automated dispersion equipment, this technology allows for precise ingredient introduction at ideal intervals, promoting thorough blending and reducing the risk of ingredient segregation.
Ensuring Quality Control in Powder Blending
Quality control is essential in powder blending to ensure that homogeneity meets the required specifications. Several techniques are commonly employed to verify blend uniformity, including:
- Sampling and Analysis – Regular sampling during blending allows for laboratory testing to assess particle distribution and concentration.
- Spectroscopy – Near-infrared (NIR) and Raman spectroscopy provide non-destructive testing methods to assess blend uniformity and ensure ingredient dispersion without disrupting the blend.
- Particle Imaging – High-resolution particle imaging technology allows for detailed analysis of particle size and distribution within a blend, providing insights into the uniformity of the mixture.
These quality control methods, combined with advanced blending techniques and equipment, enable manufacturers to deliver high-quality, homogeneous powder blends that meet stringent industry standards.
Achieve Optimal Powder Blending with Industrial Technology Corporation
Powder blending mastery requires the right combination of equipment, expertise, and dedication to quality. Whether your industry demands precision for consistency in food production or robust performance in chemicals, achieving homogeneity is the key to success.
At Industrial Technology Corporation, we provide custom toll blending services, private labeling, and high-quality chemical formulations tailored to meet the unique needs of each client. With our expertise in powder blending and advanced blending technologies, we can help you achieve the perfect mix for your business. Contact us today to inquire about our services, request a quote, or discuss your specific blending requirements. We look forward to developing innovative solutions that drive success for your business.