Emerging Trends in Blending Technology: What to Expect in 2025
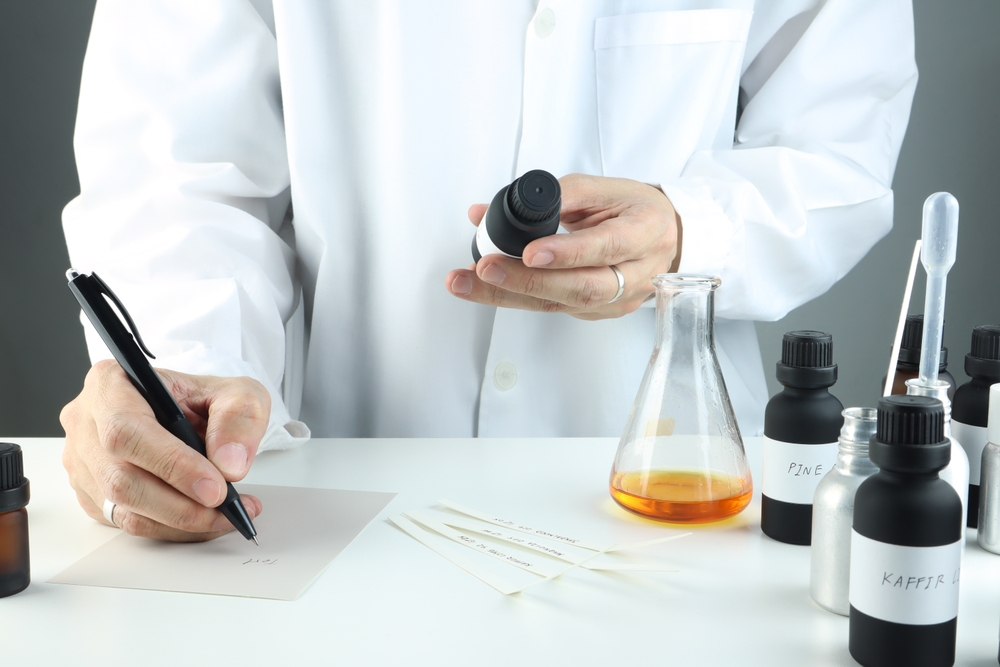
Blending technology continues to play a vital role across industrial sectors, especially in chemicals, pharmaceuticals, food production, and manufacturing. As we move into 2025, blending technology is evolving rapidly, driven by digital transformation, sustainability mandates, and automation. These emerging trends promise to transform how businesses approach formulation, production efficiency, and scalability.
Current State of Blending Technology
Blending technology today has reached a point of high efficiency, precision, and safety in controlled environments. Traditional processes involve the physical mixing of raw materials—powders, liquids, or granules—using various equipment such as ribbon blenders, paddle mixers, high-shear mixers, and static blenders.
Industrial sectors rely on blending for:
- Homogeneous mixture creation
- Customization of formulations
- Batch consistency and quality control
- Thermal and chemical process integration
Despite the substantial progress, many current systems are still reliant on operator input, subject to variability, and may lack real-time insights. Additionally, challenges remain in scaling custom formulations, reducing downtime between batches, and optimizing for sustainability.
These limitations are precisely what emerging trends seek to address through transformative technologies.
Key Trends Shaping the Future
Smart Automation and Sensor Integration
Modern blending systems are beginning to incorporate smart sensors and Industrial Internet of Things (IIoT) devices. These tools enable real-time monitoring of parameters like temperature, viscosity, particle size distribution, and blend uniformity.
How it helps:
- Reduces reliance on manual sampling
- Enables early detection of deviations
- Optimizes batch consistency and throughput
With 2025 on the horizon, we expect a broader adoption of closed-loop systems, where automated feedback from sensors adjusts blending parameters on the fly to maintain ideal conditions.
Predictive Maintenance Using AI
Predictive maintenance powered by machine learning is another growing trend. By analyzing historical equipment data, AI can predict component failures before they happen.
Benefits include:
- Avoiding costly downtime
- Extending equipment lifespan
- Reducing repair and maintenance costs
This shift from reactive to proactive maintenance is particularly valuable in high-volume toll blending operations where uptime is critical.
Digital Twins in Process Simulation
A digital twin is a virtual model of a physical system. Blending allows engineers to simulate different formulations, process parameters, and equipment setups without disrupting actual operations.
Use cases:
- Testing new chemical formulations
- Modeling heat distribution and shear forces
- Training operators in virtual environments
By 2025, expect digital twins to be a standard feature in large-scale operations, especially in facilities that require extensive regulatory documentation and validation.
Green Blending Technologies
As sustainability becomes a top priority, the blending industry is adopting eco-friendly practices. These include:
- Solventless and low-VOC formulations
- Cold blending techniques to reduce energy use
- Equipment designed for faster clean-in-place (CIP)
Suppliers are also moving toward biodegradable lubricants, recyclable packaging, and closed-loop waste recovery systems. These changes are driven by both environmental mandates and customer demand.
Modularity and Customization
Manufacturers now require more flexibility from their blending partners. Modular blending systems—designed for fast changeovers and scalability—are gaining popularity.
This trend supports:
- Custom toll blending services
- Small-batch production with rapid formulation switching
- Efficient use of space and energy
In 2025, we anticipate even greater demand for plug-and-play equipment and software that can quickly adapt to changing product lines.
Predictions for 2025 and Beyond
Innovations and Disruptions
Autonomous Blending Systems
The holy grail of blending technology is a fully autonomous system that:
- Loads raw materials via robotics
- Uses AI to monitor and control the process
- Packages the final product automatically
While not widespread yet, pilot programs for lights-out manufacturing are underway in advanced sectors like biotech and electronics. By late 2025, mid-sized manufacturers may begin integrating semi-autonomous modules, especially for repeat formulations.
Blockchain for Supply Chain Transparency
With the growing need for traceability, especially in pharma and food sectors, blockchain will become an important tool. It enables secure, tamper-proof records of:
- Source materials
- Batch records
- Quality testing
For toll blending service providers, this technology adds a competitive edge by demonstrating compliance and trustworthiness to clients.
AI-Driven Formulation Development
AI tools can analyze thousands of formulation parameters to identify optimal blends faster than human chemists. While still in its infancy, this approach can significantly reduce R&D time, particularly for custom chemical blends or high-performance coatings.
Expect hybrid labs—combining human expertise with AI suggestions—to become more prevalent in 2025.
Impact on Industry Standards
Regulatory Compliance
With automation and data analytics embedded in processes, meeting standards like ISO 9001, cGMP, REACH, and EPA regulations will become more streamlined. Real-time data logs ensure traceability and make audits easier.
Worker Safety
Smart systems that reduce manual intervention, such as automated loading and closed systems, enhance safety by minimizing exposure to hazardous materials. Expect updated OSHA protocols and compliance frameworks to reflect these technological advancements.
Quality Control
Advanced sensors will set new benchmarks for precision and consistency. Instead of random batch sampling, continuous monitoring can become the norm. This raises the bar for what constitutes “high quality” in blended products.
Preparing Your Business for Change
Conduct a Technology Audit
Review your current blending infrastructure and identify:
- Equipment that’s aging or prone to failure
- Manual steps that can be automated
- Gaps in data collection and analysis
This audit sets the foundation for prioritizing upgrades.
Partner with Technology-Forward Providers
Whether outsourcing or expanding in-house capabilities, choose partners like Industrial Technology Corporation are already leading the way by offering:
- Custom toll blending services
- Private label opportunities
- Advanced chemical formulation expertise
Invest in Workforce Training
As systems become more complex, your team must be trained to interpret sensor data, manage predictive tools, and work alongside AI-assisted systems. Cross-training across production, IT, and R&D teams can increase operational agility.
Focus on Sustainability Metrics
Regulatory and consumer pressure will only intensify. Prepare now by:
- Monitoring your carbon footprint
- Reducing water and energy usage
- Selecting greener raw materials
This can also be a strong value proposition in your marketing and client communications.
Be Future-Ready with Industrial Technology Corporation
As we approach 2025, the evolution of blending technology presents both challenges and opportunities. From smart automation and predictive analytics to blockchain integration and sustainable formulations, the landscape is transforming rapidly.
To stay competitive, businesses must embrace innovation, upgrade legacy systems, and collaborate with forward-thinking partners.
At Industrial Technology Corporation, we’re committed to being your trusted partner through this transformation. Whether you need custom toll blending services, private label opportunities, or quality chemical formulations for your business, we are here to meet your needs.
Contact us today to inquire about our services, request a quote, or discuss your specific requirements. We look forward to working with you to develop innovative solutions that drive your business’s success.