Innovations in Energy Efficiency: Reducing Costs in Industrial Mixing
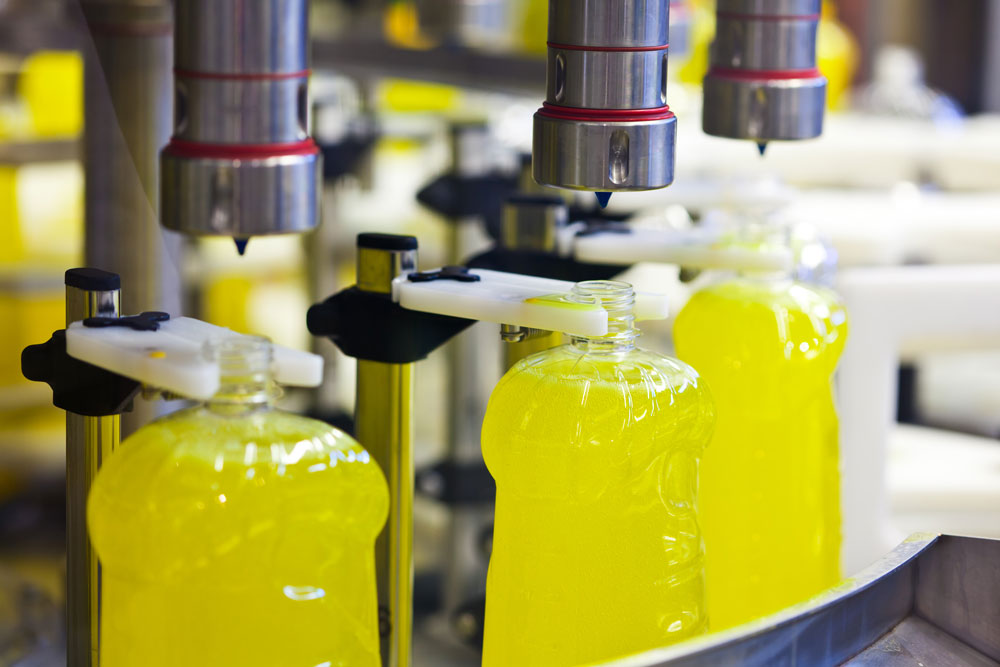
The Impact of Energy Efficiency in Mixing Processes
Energy efficiency has emerged as a critical factor in industrial operations, particularly in mixing processes where mechanical, thermal, and electrical energies intersect. In the chemical manufacturing and toll blending industries, industrial mixers are pivotal in producing consistent and high-quality formulations. However, traditional mixing systems are often energy-intensive, contributing significantly to operational costs and environmental impacts.
Modern industries are increasingly aware of the financial and ecological ramifications of energy use. Efficient energy management in mixing operations can lead to considerable cost savings, enhanced productivity, and reduced carbon footprints. By optimizing energy inputs and minimizing waste, companies can achieve sustainable growth and meet stringent regulatory requirements. For facilities engaged in toll blending or private label production, such improvements are not just optional but imperative.
A major driver of inefficiency in mixing comes from suboptimal process design, including oversized equipment, prolonged mixing times, and inadequate control systems. Implementing energy-efficient solutions enables businesses to fine-tune these aspects, ensuring the delivery of high-quality blends with minimal energy expenditure.
Innovative Technologies for Reducing Energy Consumption
The past decade has witnessed significant advancements in technology aimed at improving energy efficiency in industrial mixing. These innovations not only reduce electricity consumption but also enhance process control, product uniformity, and equipment longevity.
Variable Frequency Drives (VFDs)
Variable Frequency Drives (VFDs) are among the most impactful technologies in reducing energy use in mixing. VFDs allow operators to precisely control motor speed, aligning power output with the specific demands of each mixing operation. By avoiding full-speed operation during lower-load scenarios, VFDs significantly cut energy waste and mechanical wear.
High-Efficiency Motors
Replacing standard motors with high-efficiency or premium-efficiency motors can yield substantial energy savings. These motors are designed with improved core materials and tighter manufacturing tolerances, resulting in lower electrical losses. When paired with intelligent motor control systems, they can offer a 5-10% improvement in energy use compared to traditional counterparts.
Advanced Mixing Impellers
Modern impeller designs, such as hydrofoil and axial flow impellers, are engineered to achieve greater mixing performance at lower power inputs. These impellers reduce torque and shear forces while maintaining blend uniformity, making them ideal for energy-conscious applications.
Inline and Continuous Mixers
Inline and continuous mixing systems eliminate the need for batch processing, reducing idle time and unnecessary energy consumption. These systems maintain a steady-state operation, improving throughput while using less energy per unit of product.
Economic Benefits of Energy-Efficient Operations
Energy-efficient practices offer more than just sustainability; they are a cornerstone of operational excellence and profitability. In a highly competitive market, the ability to produce quality blends at lower costs provides a tangible business advantage.
Reducing energy consumption directly lowers utility bills, which can account for a substantial portion of total production costs. Over time, investments in efficient technologies can result in rapid returns, often with payback periods of less than three years.
Moreover, energy efficiency contributes to:
- Lower Maintenance Costs: Efficient systems endure less wear and tear, extending equipment lifespan and reducing downtime.
- Increased Throughput: Technologies like continuous mixers and automation allow for faster processing with less energy input.
- Regulatory Compliance: Meeting or exceeding government energy standards can lead to tax credits, grants, and favorable financing.
- Enhanced Reputation: Demonstrating a commitment to sustainability can improve brand perception and customer loyalty.
Energy Audits and Assessments
Conducting comprehensive energy audits is a foundational step toward improving energy efficiency. These assessments identify energy drains, quantify losses, and highlight opportunities for cost-effective upgrades. A detailed audit typically involves:
- Reviewing historical energy consumption data
- Inspecting equipment and operational practices
- Identifying inefficiencies in motor systems, controls, and thermal management
- Recommending actionable solutions tailored to the specific mixing process
Professional audits can reveal hidden inefficiencies and guide decision-makers in prioritizing interventions that offer the greatest ROI.
Case Studies of Successful Implementations
Case Study 1: Chemical Toll Blender in the Midwest
A chemical toll blending facility implemented VFDs across all mixer motors and upgraded to premium-efficiency motors. Coupled with real-time energy monitoring, the facility reduced energy consumption by 18%, saving over $100,000 annually. The return on investment was realized in just 18 months.
Case Study 2: Food Ingredient Manufacturer
Switching from batch mixing to a continuous inline system allowed a food-grade ingredient producer to reduce mixing times by 40%, energy use by 22%, and product waste by 15%. The company also saw an improvement in product consistency and throughput.
Case Study 3: Paint and Coatings Producer
A coatings company replaced its outdated impellers with advanced hydrofoil designs and incorporated sensor-driven automation. The result was a 12% reduction in energy usage and a 25% reduction in quality control rework due to improved batch uniformity.
These examples underscore the significant gains available to businesses that embrace energy-efficient technologies in their mixing operations.
Future Innovations in Energy Efficiency
As Industry 4.0 continues to evolve, the future of energy efficiency in industrial mixing looks even more promising. Several emerging technologies and trends are poised to revolutionize energy use across the sector.
Artificial Intelligence and Machine Learning: AI can analyze vast datasets from sensors and control systems to predict optimal mixing conditions, anticipate maintenance needs, and minimize energy use dynamically.
Digital Twins: Virtual replicas of mixing systems enable real-time simulation and optimization of processes, allowing engineers to test energy-saving strategies before implementation.
Decentralized Energy Systems: On-site renewable energy generation, such as solar and wind, integrated with energy storage systems, can power mixing operations independently, reducing reliance on the grid.
Magnetically Coupled Mixers: These systems eliminate the need for mechanical seals and reduce friction losses, making them more energy-efficient and maintenance-friendly.
Biodegradable Process Aids: Using biodegradable surfactants and thickeners can lower the energy required to achieve target viscosities and improve blending efficiency, particularly in emulsions.
These innovations point toward a more resilient, adaptive, and sustainable future for industrial mixing.
Partner with Industrial Technology Corporation Today
At Industrial Technology Corporation, we understand the critical importance of energy efficiency in today’s industrial landscape. Whether you need custom toll blending services, private label opportunities, or quality chemical formulations for your business, we are here to meet your needs with precision, reliability, and sustainability at the forefront.
Our team leverages state-of-the-art equipment, industry best practices, and a deep commitment to operational excellence to deliver solutions that align with your energy efficiency goals. Simply contact us today to inquire about our services, request a quote, or discuss your specific requirements. We look forward to working with you to develop innovative solutions that drive your business’s success.