Revolutionizing Industrial Blending with IoT and AI Integration
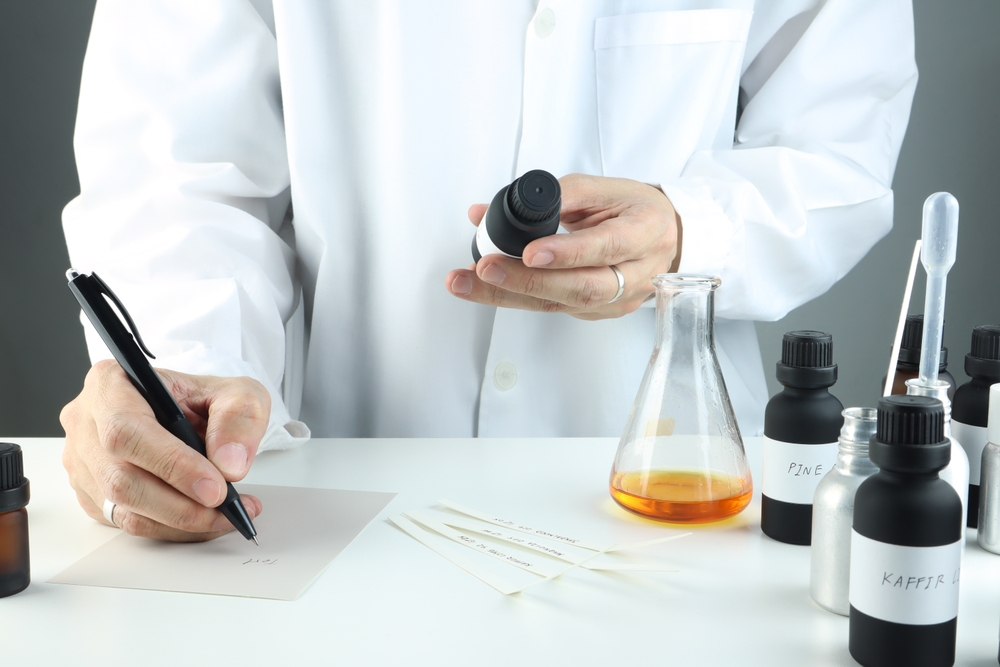
The Rise of Industrial IoT in Blending
Industrial blending has long been a cornerstone of the chemical, pharmaceutical, food, and materials industries. As businesses seek greater efficiency, consistency, and adaptability, the integration of Industrial IoT (Internet of Things) technologies has become a game-changing solution. These innovations are transforming traditional batch and continuous blending operations into intelligent, data-driven systems capable of real-time decision-making and performance optimization.
Industrial IoT enables the collection and transmission of critical data points from machinery, sensors, and operational systems across the blending process. This includes parameters such as temperature, pressure, viscosity, mixing speed, and more. With seamless connectivity between hardware and software platforms, plant managers and engineers can monitor operations remotely, automate adjustments, and maintain peak performance standards around the clock.
Current Technology Trends
Among the most impactful IoT innovations in blending are:
- Smart Sensors and Actuators: These devices monitor blend homogeneity, ingredient ratios, and environmental variables in real time.
- Edge Computing: By processing data at the machine level, edge computing reduces latency and allows for rapid decision-making without relying solely on cloud infrastructure.
- Wireless Connectivity Protocols: LoRaWAN, MQTT, and 5G networks enable stable and secure communication across large-scale facilities.
- Digital Twins: Virtual models of blending equipment allow engineers to simulate performance scenarios and predict outcomes based on real-time data.
- Integrated SCADA Systems: These supervisory control and data acquisition platforms provide unified dashboards for controlling and visualizing all aspects of the blending process.
IoT serves as the nervous system of the smart factory, ensuring that every component in the blending process is responsive, measurable, and adaptable.
Benefits of AI-Driven Blending Processes
While Industrial IoT provides the infrastructure for real-time data acquisition, Artificial Intelligence (AI) leverages that data to deliver insights, predictions, and automated optimizations. The synergy between IoT and AI yields measurable advantages across the production lifecycle.
Improved Accuracy and Consistency
AI algorithms analyze historical and real-time blending data to identify subtle patterns and inconsistencies. This capability helps minimize human error, detect anomalies, and standardize formulations to reduce batch-to-batch variability. The result is a highly reliable output that meets stringent quality control requirements.
Predictive Maintenance and Reduced Downtime
By using machine learning models trained on sensor data, AI can anticipate equipment failures and maintenance needs before they disrupt production. Predictive maintenance scheduling reduces unplanned downtime, extends machinery lifespan, and enhances operational efficiency.
Energy and Resource Efficiency
AI-optimized blending systems reduce raw material waste by fine-tuning process parameters such as mixing speed, ingredient feed rate, and temperature. These optimizations translate into energy savings, cost reductions, and more sustainable operations.
Enhanced Product Development
Data-driven insights enable research and development teams to test and iterate on new formulations more quickly. AI can simulate ingredient interactions, predict outcomes, and identify optimal blends without the need for extensive physical trials.
Real-Time Quality Assurance
In-line quality assurance powered by IoT and AI enables immediate detection of deviations from target specifications. This allows corrective actions to be implemented during production, not after a defective batch has been completed.
Real-World Case Studies
Case Study 1: Chemical Blending Automation: A multinational chemical manufacturer implemented an Industrial IoT framework integrated with AI to monitor and control their batch blending lines. The system used smart sensors and predictive algorithms to track blend uniformity, temperature thresholds, and agitation speeds. As a result, the company reduced product recalls by 25% and lowered energy consumption by 15%.
Case Study 2: Food Industry Implementation: A large food ingredients company adopted AI-driven analytics to refine its flavor and nutritional supplement blends. The AI software analyzed historical taste profiles and consumer feedback to propose formula improvements. Simultaneously, IoT sensors ensured compliance with safety standards. This approach shortened the R&D timeline by 40% and boosted product acceptance rates.
Steps to Implement IoT Solutions in Your Facility
Transitioning to an IoT- and AI-enabled blending environment requires a strategic and phased approach. Below are practical steps for successful implementation:
Step 1: Evaluate Your Current Infrastructure
Conduct a comprehensive audit of existing blending equipment, control systems, and data collection capabilities. Identify bottlenecks, outdated technologies, and areas for improvement.
Step 2: Define Operational Goals
Establish clear objectives such as reducing batch cycle time, enhancing traceability, improving yield, or minimizing equipment downtime. These goals will shape your IoT strategy and help measure success.
Step 3: Select Compatible IoT Hardware
Choose industrial-grade sensors, actuators, and controllers compatible with your blending systems. Ensure that the selected hardware supports open communication protocols and robust security features.
Step 4: Integrate Data Management Platforms
Implement SCADA systems, PLCs, or cloud-based solutions capable of aggregating, processing, and visualizing sensor data. These platforms serve as the backbone for monitoring and decision-making.
Step 5: Implement AI Tools
Use AI software solutions to analyze incoming data and optimize blending parameters. Machine learning models can be trained using historical data to forecast outcomes and recommend process adjustments.
Step 6: Train Staff and Build a Digital Culture
Educate plant operators, engineers, and decision-makers on how to use new systems. Promote a culture of digital innovation and data-driven decision-making throughout the organization.
Step 7: Monitor, Iterate, and Scale
Begin with a pilot project and monitor performance metrics closely. Use feedback loops to refine the system and gradually scale the solution across additional production lines or facilities.
Future Outlook and Innovations
The convergence of Industrial IoT and AI in blending processes is only beginning. Several exciting trends and advancements are on the horizon:
Autonomous Blending Systems
Future blending platforms will require minimal human intervention. Autonomous systems will use AI to determine optimal ingredient proportions, dynamically adjust variables, and self-correct in real time based on sensor feedback.
Blockchain Integration for Supply Chain Transparency
Combining blockchain technology with IoT will allow companies to trace raw material origin, monitor transportation conditions, and verify batch authenticity with tamper-proof records. This is particularly valuable in industries like pharmaceuticals and food.
Augmented Reality (AR) and Virtual Reality (VR)
AR/VR applications will be used for equipment training, maintenance visualization, and remote diagnostics. Operators will interact with digital overlays that guide them through complex blending system procedures.
Collaborative Robotics (Cobots)
Cobots will work alongside human technicians to manage ingredient loading, perform quality inspections, and maintain consistent operational tempos. These robots will be equipped with AI vision systems and safety-enhancing features.
Environmental Monitoring and Compliance
IoT-enabled blending systems will automatically track emissions, effluents, and other environmental indicators, ensuring compliance with sustainability regulations. AI will provide alerts and corrective action plans to stay within permissible limits.
Partner with Industrial Technology Corporation to Innovate Your Blending Operations
Call on Industrial Technology Corporation (ITC) whether you need:
- Custom toll blending services
- Private-label formulation solutions
- High-quality chemical blending expertise
We provide the technology and expertise to help your business stay ahead in a competitive marketplace.
Let us help you harness the power to elevate your blending requirements. Our team of professionals is ready to tailor solutions that meet your production and business goals.
Contact us today to inquire about our services, request a quote, or discuss your specific requirements. We look forward to working with you to develop innovative solutions that drive your business’s success.