The Art of Custom Formulation Development: From Concept to Reality
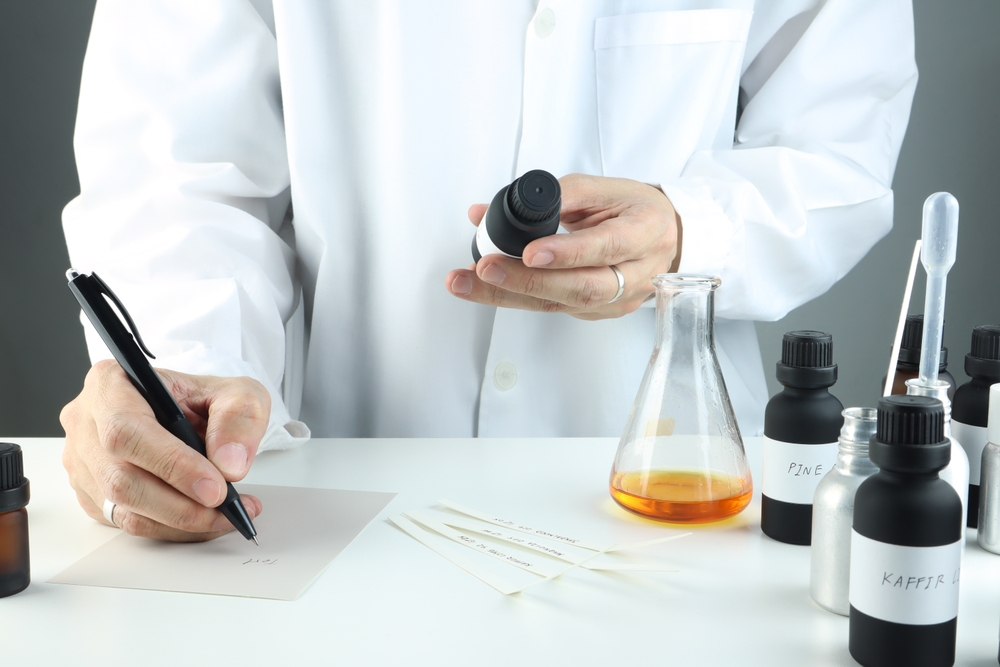
In today’s industrial landscape, custom formulation development is at the core of countless industries, from household goods to paints and coatings and beyond. The ability to transform a concept into a viable, market-ready product relies on rigorous processes, scientific expertise, and technical precision. Each step in formulation development, from initial ideation to final blending, is a collaborative journey that ensures product integrity, quality, and consistency.
Step 1: Ideation and Initial Concept Development
The first stage in custom formulation development is generating and refining the initial concept. This is the phase where product goals, target specifications, and functional requirements come together. Typically, this process begins with a collaborative meeting between the client and a skilled formulation team to discuss core questions:
- What is the purpose of the product?
- What unique benefits or characteristics should it offer?
- What environmental, regulatory, or safety considerations are essential?
Understanding the end-use application is crucial at this stage. Whether it’s a specialized cleaning agent or a unique paint formulation, the desired qualities and performance parameters need to be clearly outlined. A comprehensive concept brief outlining objectives, limitations, and target characteristics sets a solid foundation for the next steps in the formulation process.
Step 2: Research and Ingredient Selection
With a defined concept in place, the next step is to identify suitable ingredients that will deliver the required properties. This phase involves extensive research, where scientists analyze each potential component, ensuring it meets specific safety, performance, and regulatory requirements.
Ingredient selection is a crucial aspect of custom formulation. Some of the key factors considered include:
- Functionality: Each ingredient must contribute to the desired performance, such as stability, efficacy, or sensory attributes.
- Compatibility: The ingredients must interact well without causing unwanted reactions or diminishing performance.
- Cost-Effectiveness: Ingredient cost can influence the final product price, so an optimal balance between quality and affordability is sought.
- Sustainability and Environmental Impact: Clients are increasingly seeking formulations with a reduced environmental footprint, favoring renewable or biodegradable components.
The choice of ingredients ultimately shapes the product’s identity, making this phase both creative and scientific.
Step 3: Prototype Formulation and Testing
Once the ingredients are chosen, prototype formulations are created. This is a critical experimental phase where the formulation is tested for viability. Using specialized equipment and precise chemical blending techniques, initial batches are mixed to evaluate various attributes, including stability, efficacy, and overall performance.
Testing ensures that the prototype formulation meets the intended specifications. Some common tests include:
- Stability Testing: Ensures the formulation maintains its integrity over time under various environmental conditions.
- Performance Testing: Evaluates whether the product performs as intended in its real-world application.
- Safety and Toxicology Testing: Identifies potential risks or side effects associated with the formulation.
- Shelf Life Testing: Determines the product’s lifespan and how it responds to factors like temperature, light, and humidity.
This stage often requires multiple iterations, with formulators adjusting concentrations, ingredient ratios, or processing methods to achieve the best possible outcome.
Step 4: Scale-Up and Pilot Production
Once a stable, effective formulation is achieved, the next phase involves scaling up to pilot production. This phase tests whether the formulation can be reliably reproduced on a larger scale without compromising quality or performance.
Scaling up a formulation is a complex process that involves:
- Adjusting for Manufacturing Processes: Laboratory-scale mixing techniques often differ from large-scale blending methods, requiring adjustments to maintain consistency.
- Equipment Calibration: Ensuring the correct calibration of equipment, such as mixers and reactors, to handle precise volumes and processing conditions.
- Batch Testing: Pilot batches are tested for consistency, ensuring each unit meets the same high standards set during prototype testing.
Pilot production serves as a bridge between development and full-scale production, allowing for any necessary adjustments to streamline the final blending and packaging processes.
Step 5: Full-Scale Production and Chemical Blending
After successful pilot testing, the formulation moves to full-scale production. At this stage, precise chemical blending is essential to ensure that every batch of the product matches the intended formulation. Chemical blending, especially in large volumes, requires specialized expertise to manage both the technical and regulatory complexities.
Chemical blending ensures that:
- Ingredients are Consistently Distributed: Homogeneous mixing prevents variations in product performance and quality.
- Production is Efficient and Cost-Effective: Professional toll blending facilities, like those at ITC, streamline production and reduce overhead costs.
- Safety and Environmental Standards are Met: Proper ventilation, waste disposal, and handling techniques ensure a safe, compliant production environment.
For many businesses, partnering with an experienced chemical blending service provider offers significant advantages. It allows companies to focus on product innovation while outsourcing the complexities of manufacturing.
Step 6: Quality Control and Assurance
Quality control (QC) is integral to every stage of the formulation process, but it becomes especially crucial during production. Comprehensive quality control measures ensure that each batch meets strict standards and that any deviations are identified and addressed promptly.
Key aspects of QC in chemical blending and formulation include:
- Batch Sampling: Random samples from each batch are tested to verify consistency, potency, and safety.
- Documentation and Traceability: Every aspect of production is documented, allowing for traceability in case of a product recall or regulatory review.
- Regulatory Compliance Checks: Ensuring adherence to all relevant industry regulations, such as EPA, FDA, or OSHA standards.
- Customer-Specific Standards: Custom formulations often require additional testing based on specific client requirements or industry standards.
For a company like ITC, QC protocols are a cornerstone of delivering reliable, high-quality products to clients across diverse industries.
Step 7: Packaging and Labeling
Once the product has passed all quality checks, it’s ready for packaging and labeling. Packaging serves as both a protective barrier and a brand extension, ensuring that the product reaches consumers in pristine condition and aligns with the client’s brand image.
Considerations during this stage include:
- Compatibility: Packaging materials must be compatible with the product to prevent chemical reactions or degradation.
- Environmental Impact: Many companies are moving toward sustainable packaging options, such as recyclable materials or reduced plastic use.
- Regulatory Compliance: Labeling must comply with industry regulations and provide accurate information about ingredients, usage, and safety.
Proper packaging and labeling play an essential role in product perception and shelf appeal, influencing consumer trust and brand loyalty.
Step 8: Launch and Post-Launch Support
With packaging and labeling finalized, the product is ready for market launch. However, the role of a custom formulation provider like ITC doesn’t end here. Post-launch support can be vital, particularly in the early stages, when initial feedback from the market is gathered.
Post-launch services may include:
- Formulation Adjustments: Based on customer feedback or emerging trends, minor formulation tweaks may be necessary to maintain product relevance.
- Troubleshooting: If production or performance issues arise, the formulation team can troubleshoot and resolve these issues.
- Product Scaling and Optimization: As demand grows, further scale-up may be necessary to ensure the product remains cost-effective and efficient.
The Importance of Partnering with a Reliable Custom Formulation Provider
Custom formulation development is a multi-stage process that requires precision, technical expertise, and the ability to adapt to evolving industry trends. For businesses, partnering with an experienced provider like ITC offers the assurance of high-quality, reliable formulations that meet specific needs.
At ITC, our toll blending and formulation services are designed to take your concept from the lab to reality with complete attention to detail and quality. With our state-of-the-art facilities, extensive experience, and commitment to excellence, we support companies in realizing their product vision and achieving success in competitive markets.
Why Choose Industrial Technology Corporation for Custom Formulation and Chemical Blending?
Whether you’re in need of custom toll blending services, private label opportunities, or quality chemical formulations for your business, Industrial Technology Corporation (ITC) is here to meet your needs. Our team of scientists and technicians specializes in every aspect of the formulation process, ensuring that your product meets the highest standards of performance, safety, and quality.
Simply contact us today to inquire about our services, request a quote, or discuss your specific requirements. We look forward to working with you to develop innovative solutions that drive your business’s success.